Specialized in automated OSB, MGO, and aluminum sandwich panel equipment for fire-proof, energy-efficient construction.
Our SIP panel machine (Structural Insulated Panel Machine) is advanced equipment designed to produce lightweight, high-strength sandwich panels for construction applications. These panels combine rigid foam insulation (e.g., EPS, XPS, PU) with outer layers of OSB, MGO board, aluminum, or PVC to create energy-efficient, load-bearing structures.
Table of Contents
Main Types Of Sip Panel Machine Supplied by DEYI
1. Fire-Proof Door SIP Panel Press Machine & OSB Exterior Manufacturing Equipment
Our fire-proof door SIP panel press machine produces Class A-rated panels for commercial safety. Paired with OSB SIP panel exterior equipment, it ensures weather-resistant, load-bearing walls for modular homes.
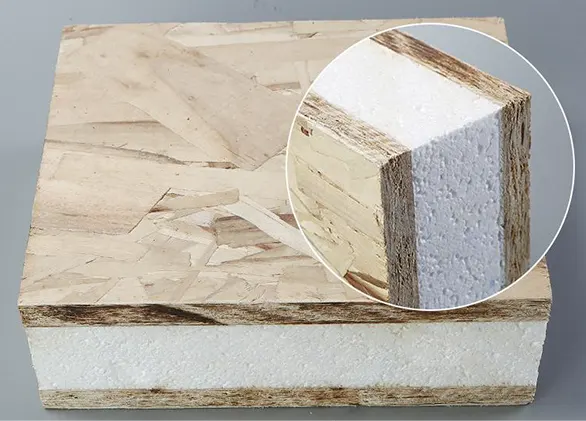
2. EPS/XPS & MGO Sandwich Panel Machines for Sustainable Construction
The EPS/XPS SIP panel glue making machine combines lightweight insulation with automated glue application, while our MGO EPS XPS sandwich panel machine delivers fire-resistant, moisture-proof structures ideal for industrial use.
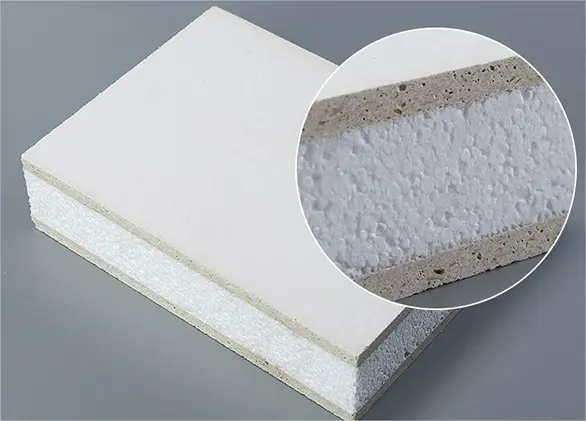
Why Choose Our Professional SIP Panel Machinery?
- Automated Precision: CNC cutting and PLC control for ±0.5mm accuracy in SIP panel press machines.
- Material Flexibility: Handle EPS, XPS, OSB, MGO, and PIR in SIP sandwich panel machines.
- Energy Efficiency: Reduce electricity costs by 40% with vacuum lamination technology.
How to Make SIP Panels: A Precision-Driven Production Process
Crafting high-performance SIP (Structural Insulated Panels) requires advanced equipment and strict technical standards. At DEYI, we leverage professional SIP panel machines to ensure every panel meets superior quality benchmarks. Here’s our streamlined production process:
1. Material Preparation – The Foundation of Quality
- Core Materials: Select premium insulation cores like EPS, XPS, or PIR. Our machinery handles diverse materials, including eco-friendly recycled EPS for sustainable solutions.
- Facing Materials: Prepare OSB, MGO board, or aluminum integrated plates. These layers are cut to precise dimensions using our automated cutting systems, ensuring seamless fit for wall, roof, or fire-proof door applications.
2. Glue Application – Strong Bonds, Lasting Durability
- Utilize our EPS SIP panel glue making machine or specialized glue systems. High-precision nozzles apply structural adhesive evenly on insulation cores and facing materials, laying the groundwork for robust panel integration.
3. Pressing & Bonding – Shaping Structural Integrity
- Assemble the sandwich structure: insulation core between two facing layers. Our SIP panel press machine (like the fire-proof door SIP panel press) applies uniform pressure, curing the glue under controlled conditions. This step ensures panels achieve Class A fire ratings (for fire-proof models) or exceptional load-bearing capacity for construction use.
4. Finishing & Cutting – Precision to the Millimeter
- Post-bonding, panels enter CNC cutting stations. Whether it’s trimming edges for OSB SIP panel exteriors or customizing sizes for aluminum integrated plate sandwich panels, our equipment ensures ±0.5mm accuracy, meeting diverse project requirements.
5. Quality Inspection – Zero-Compromise Standards
- Every panel undergoes rigorous testing:
- Thermal Performance: Verify U-values (e.g., PIR-insulated roof panels achieving ≤0.15 W/m²·K).
- Mechanical Strength: Test load-bearing capacity and impact resistance.
- Fire/Safety Compliance: Ensure MGO-based panels meet fire-resistant standards or EPS panels align with eco-friendly certifications.
6. Packaging & Delivery – Ready for Your Projects
- Finally, panels are carefully packaged to prevent transit damage. Whether it’s MGO EPS sandwich panels for industrial buildings or PIR-insulated roof panels for premium projects, we ensure timely delivery, supporting your construction timelines.
Why choose us?
Single-Component PU Adhesive Metering & Coating Equipment
- Precise Metering: Ensure accurate adhesive dosage with ±1% precision.
- Stable Coating: Uniform glue distribution across various substrates.
- User-Friendly Operation: Intuitive PLC control interface.
- Automatic Feeding: Continuous material supply system.
- High Automation: Reduce manual intervention with integrated workflows.
Available in multiple width and length configurations (e.g., 1.2m/2.4m/3.6m widths) to accommodate diverse production needs.
Glue out amount | 0-6000g/min |
A B glue ratio accuracy | Ratio accuracy: ≤ ±2% (such as 100:25 ±2) |
Air Source | 0.6-0.8Mpa |
Power supply | 380v 50Hz |
Device power | 10kw |
Equipment size | 12m*2.4m*2.2m |
Flow accuracy | ≤ ± 3% |
Proportioning | Adjustable from 1:1 to 5:1 |
Production rate | 12m/min gluing speed is adjustable |
Glue viscosity range | A glue ≤30000mpa.s (ambient temperature 24℃) |
Ideal for bonding flat materials (ceramic granite, metal, HPL, PVC sheets, OSB boards, MGO boards, fiberboard) with insulation materials (PIR, PUR, EPS, XPS) using single-component PU adhesives.

Advantages of Cold Press Machines in SIP Panel Production
Cold press machines play a critical role in manufacturing high-quality, energy-efficient SIP panels by bonding insulation cores (EPS, XPS, PIR) with facing materials (OSB, MGO, aluminum) under ambient temperature
1. Energy Efficiency & Cost Savings
- No Heating Required: Avoid energy-intensive heating systems, reducing electricity costs by 30-50% compared to hot press machines.
- Lower Maintenance: Simplified mechanical design minimizes downtime and repair expenses.
2. Material Compatibility
- Thermal Stability: Ideal for heat-sensitive cores like EPS (melting point ~240°C), preserving insulation properties.
- Versatile Facing Options: Works with OSB and aluminum without warping or delamination.
3. Precision Bonding
- Uniform Pressure Distribution: Hydraulic or vacuum systems ensure consistent bonding strength (≥1.5 MPa) across large panels (e.g., 12m lengths).
- Edge Quality: Advanced trimming systems achieve ±0.5mm accuracy for seamless installations
4. Ideal for Specialized Applications
- Fire-Resistant Panels: Maintains MGO board integrity during bonding for Class A fire-rated SIPs.
- Insulated Roof Systems: Ensures PIR cores retain thermal efficiency (U-value ≤0.15 W/m²·K).
- Marine/Refrigeration Use: Bonding compatible with moisture-resistant materials (e.g., aluminum + XPS).3