gypsum block machine
Fully automatic gypsum block machine revolutionizes lightweight partition production using gypsum and water. This gypsum block manufacturing equipment combines precision engineering with smart automation to deliver consistent, high-quality gypsum hollow blocks for modern construction needs.
Gypsum Block Making Machine
Types Of gypsum block making machine
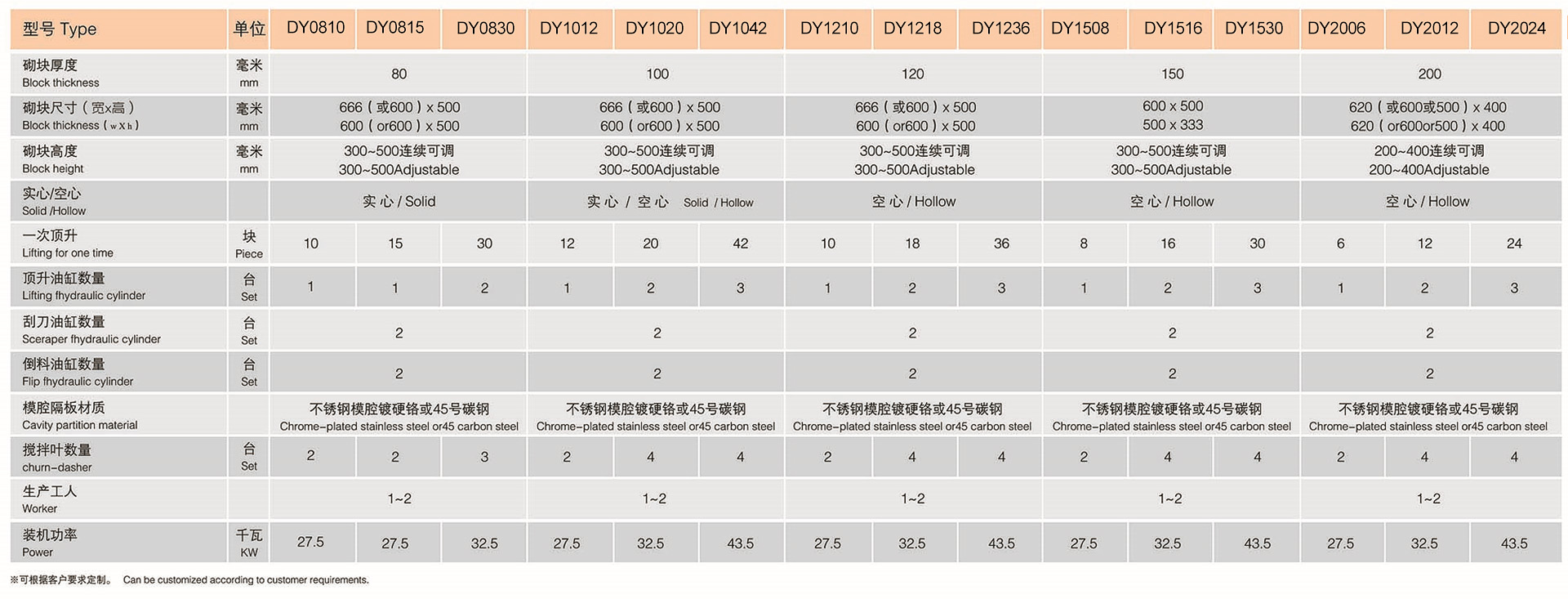
How to make gypsum blocks?
Our gypsum block manufacturing equipment combines cutting-edge technology and precision engineering to deliver high-quality lightweight hollow blocks for construction applications. Below is a detailed breakdown of the automated production process:
1. Dosing System
The dosing system ensures precise material ratios for consistent block quality:
- Water metering device and powder metering device (gypsum, additives) with compressed air systems.
- Uniform mixture control prevents segregation and enhances strength.
- Ideal for gypsum hollow block equipment requiring eco-friendly materials like desulfurized gypsum.
2. Screw Convey Feeding System
Designed for smooth material flow:
- Discharge balance device and butterfly valve ensure clog-free, uniform discharge.
- Reduces manual labor in gypsum block production line operations.
- Supports scalable capacity for high-efficiency production.
3. Mixer
A high-speed mixer with stainless steel components ensures thorough blending:
- Mixing tank and stirrer with motorized pouring cylinder.
- Optimal consistency for mold filling and strength.
- Equipped with IoT-enabled intelligent control panel for real-time adjustments.
4. Forming Machine
The gypsum block forming machine transforms slurry into precise shapes:
- Hydraulic-powered molds for lightweight hollow blocks.
- Multi-specification production via quick mold changes.
- Fire-resistant and soundproof properties meet construction standards.
5. Central Hydraulic Station
Provides reliable power for critical operations:
- High/low pressure oil pumps and drive motor with fuel tank (oiler, liquid level indicator).
- Electromagnetic valves and throttle valves ensure smooth mold movement.
- Essential for automated gypsum block equipment.
6. Pneumatic Flexible Fixture
Efficiently handles blocks during production:
- On-rails trolley with high/low speed movement and brake positioning.
- Ergonomic design reduces damage risks in gypsum block machinery.
- Supports modular production lines.
7. Automatic Control System
A PLC-based control system ensures seamless operation:
- Button box and electric control cabinet for user-friendly monitoring.
- Real-time data tracking and remote adjustments via IoT integration.
- Enhances safety in gypsum block manufacturing.
Why choose us?
- Sustainable: Utilizes industrial waste like phosphogypsum for green construction.
- Cost-Effective: Reduces labor and energy costs with automated processes.
- Versatile: Produces blocks for interior partitions, fire-resistant barriers, and more.
Advantages | Experience |
Our experience | over 300projects in China, all over the world |
Formula | we will provide a unique formula, can save your much cost |
Cavity quantity | 4~52cavities per mould.The largest, most advanced technology in China. |
Different sizes | organized into only one mould, No factory can achieve such level |
Mixer | no need power, our unique design. save your electricity much |
What we provide | For your project |
Free design | we will provide free design for you, including plant layout; machinery diagram, equipmentlist, ect. |
Labor shifts | arrangement suggestions |
Raw material supports | we supply all surports for raw material supplier information |
Installation | our process/ installation/ electricity engineers will stay at your plant until your workers know how to produce good products. |
Testing | after installation, we will test your production, and sign agreement with your workers after succesfully testing. |
After-sale service | we will be here for 24hours. When you need any help, just contact us! |
Key Features
Our gypsum block drying kiln features a single-channel tunnel design with optimized airflow and temperature control, ensuring efficient curing for lightweight hollow blocks. This energy-efficient drying system is ideal for automated gypsum block production lines, delivering consistent quality and high throughput.
1. Structure & Heat Source
- Tunnel Kiln Design: Bottom air inlet and top air outlet configuration maximizes heat distribution.
- Diesel Burner System: Provides reliable flame heat exchange for uniform drying.
- Centrifugal Fan Circulation: Forced air circulation ensures rapid moisture evaporation.
- Independent Moisture Drainage: Prevents condensation buildup in gypsum block equipment.
2. Air Circulation System
- Forced Large-Flow Hot Air: Directional circulation with independent temperature and airflow controlenhances drying efficiency.
- Underfeed Air Supply: Fans blow hot air into ducts from the tail, distributing evenly via perforated air distribution plates for bottom-to-top airflow.
- Top Exhaust System: Moisture-laden air is extracted by roof-mounted exhaust fans after exchanging with wet blocks.
3. Kiln Car Handling
- Steering & Jacking Device: Enables seamless kiln car rotation and positioning for continuous operation.
- Dual-Lane Configuration:
- Empty Car Back Lane: Returns empty kiln cars to the loading station.
- Heavy Truck Unloading Lane: Efficiently removes dried blocks from the kiln.
4. Key Advantages
- Uniform Drying: Precise airflow and temperature control eliminate warping in gypsum hollow blocks.
- High Capacity: Supports 4~52cavities per mould for large-scale gypsum block manufacturing.
- Low Maintenance: Durable stainless steel components and modular design reduce downtime.
Applications of Gypsum Blocks in Modern Construction
Gypsum blocks are versatile, eco-friendly building materials widely used in residential, commercial, and industrial projects. Here’s how they enhance construction efficiency and sustainability:
1. Interior Partitions & Walls
- Scenarios: Offices, hotels, apartments, schools.
- Advantages:
- Lightweight: Reduce structural load by 30% compared to traditional masonry.
- Soundproofing: Blocks with 100-150mm thickness achieve 40-50dB noise reduction.
- Fast Installation: Dry construction method cuts labor time by 50%.
2. Fire-Resistant Barriers
- Scenarios: Fire-rated walls, stairwells, electrical room enclosures.
- Advantages:
- Class A Fire Rating: Withstand fire for ≥3 hours (ASTM E119 certified).
- Non-Toxic: No harmful fumes released during combustion.
3. Industrial & Infrastructure Projects
- Scenarios: Factory floors, underground tunnels, wastewater treatment plants.
- Advantages:
- Moisture Resistance: Ideal for humid environments (water absorption ≤8%).
- Chemical Stability: Resist corrosion from acids/alkalis in industrial settings.
4. Decorative & Architectural Elements
- Scenarios: Feature walls, ceilings, cultural centers.
- Advantages:
- Smooth Surface: Directly paint, tile, or apply decorative finishes.
- Customizable: Available in textures, colors, and shapes for artistic designs.
5. Green & Sustainable Construction
- Scenarios: LEED-certified buildings, energy-efficient homes.
- Advantages:
- Eco-Friendly: Made from 90% recycled materials (e.g., desulfurized gypsum).
- Low Carbon: Reduce CO₂ emissions by 40% compared to concrete.
Contact us
Got Questions? Let’s Build Your Success Together
Transform Your Construction Business with Automated Gypsum Block Solutions