Gypsum Board Production Line
Gypsum board production line from our company is designed to deliver high-quality plasterboard products for the construction industry. Engineered with precision, this gypsum board making machine combines cutting-edge technology and robust components to ensure seamless production of gypsum boards, catering to diverse market demands
Table of Contents
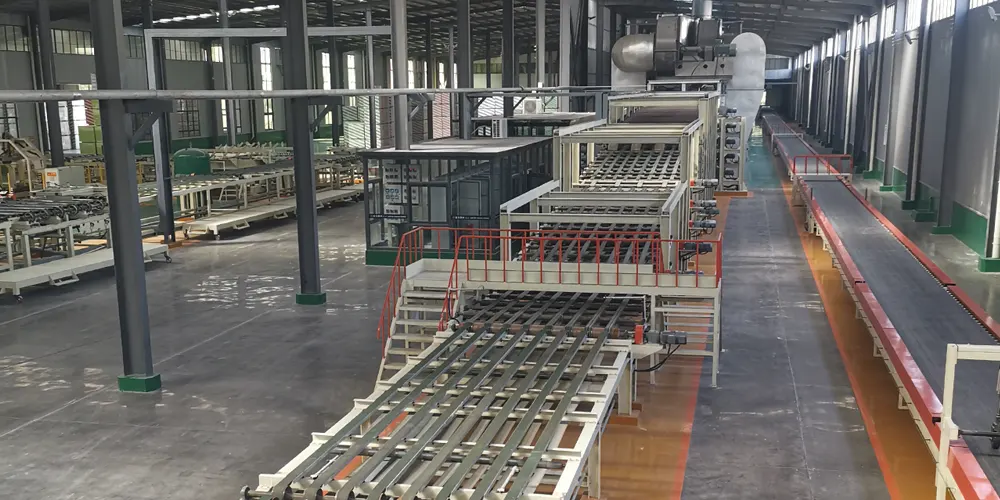
Annual output of 5 million square meters-30 million square meters
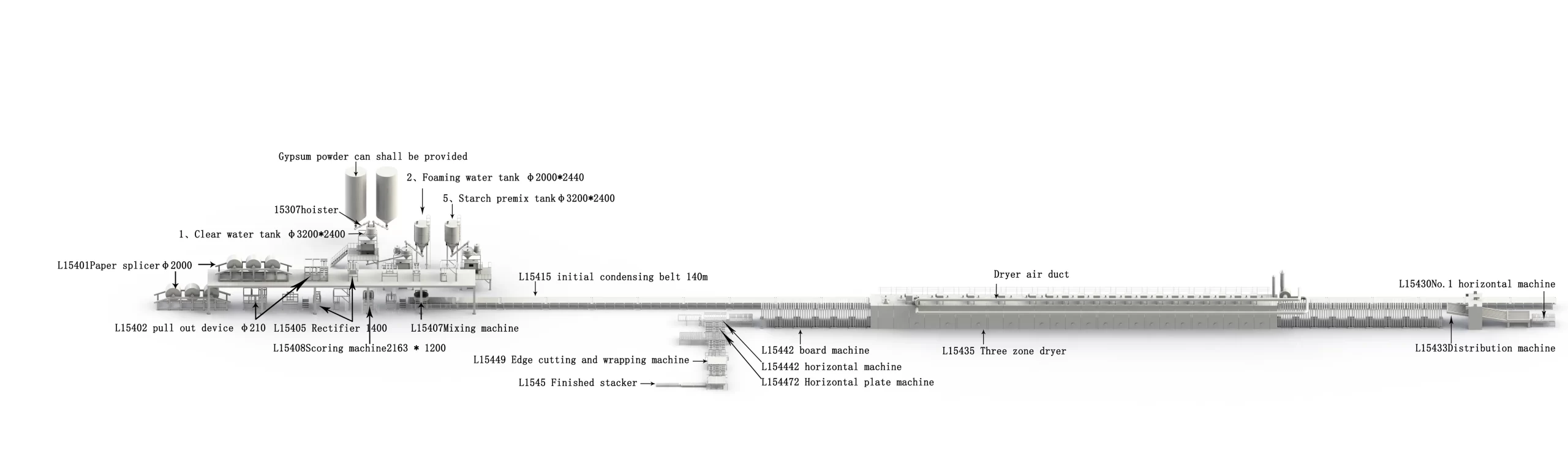
Plasterboard Production Line Key Features:
- Fully Automated Process: From raw material mixing (gypsum slurry, paper, additives) to forming,drying, and cutting, our gypsum board machine streamlines every step for maximum efficiency.
- Versatile Output: Produces standard plasterboard (paper-faced), fire-resistant, moisture-proof, and decorative boards, ideal for walls, ceilings, and partitions.
- High Throughput: Capable of manufacturing up to [X] square meters per hour, ensuring rapid project completion.
- Customizable Machinery: Adaptable to produce various board thicknesses (6mm–25mm) and sizes, meeting global standards.
The Type Of Paper face plasterboard Line
The following shows the parameters of corresponding production lines according to different production capacities. You can consult information about relevant production lines based on your factory building, budget and production capacity requirements.
capacity(10,000 m²) | line size(m) | factroy size(m) | container quantity(40′ container) | initial setting speed(m/min) |
100 | 80*15 | 100*20 | 6 | 2 |
200 | 100*15 | 120*20 | 8 | 4 |
300 | 110*15 | 130*20 | 10 | 6 |
400 | 120*20 | 140*30 | 12 | 8 |
500 | 140*20 | 160*30 | 15 | 10 |
600 | 150*25 | 170*30 | 17 | 12 |
700 | 160*32 | 190*40 | 19 | 14 |
800 | 170*32 | 200*40 | 22 | 16 |
900 | 180*32 | 210*40 | 26 | 18 |
1000 | 190*32 | 240*40 | 30 | 20 |
1200 | 210*32 | 260*40 | 33 | 24 |
1500 | 250*32 | 300*40 | 38 | 30 |
1800 | 280*32 | 350*40 | 41 | 36 |
2000 | 320*32 | 380*40 | 45 | 40 |
2500 | 350*42 | 430*50 | 52 | 50 |
3000 | 380*42 | 450*50 | 60 | 60 |
Product Applications
The gypsum boards manufactured by our production line are versatile and widely used in various industries. Here’s a detailed breakdown:
1. Construction Sector
- Residential Buildings: Ideal for interior partitions, ceilings, and wall systems in homes, creating functional and aesthetic living spaces.
- Commercial Properties: Used in offices, shopping malls, hotels, and other commercial buildings for wall cladding and ceiling installations to enhance visual appeal and space efficiency.
2. Functional Solutions
- Fire-Resistant Areas: Fire-rated gypsum boards are applied in fire-resistant partitions, stairwells, and elevator shafts to provide safety and compliance with building codes.
- Moisture-Prone Environments: Moisture-resistant gypsum boards are suitable for kitchens, bathrooms, and basements, preventing damage from humidity.
3. Acoustic & Thermal Insulation
- Soundproofing: Used in recording studios, cinemas, and conference rooms to reduce noise transmission and improve acoustic quality.
- Thermal Efficiency: Integrated into exterior wall systems and roofing to enhance energy efficiency by minimizing heat transfer.
Our gypsum boards combine durability, versatility, and cost-effectiveness, making them a preferred choice for modern construction and design projects.
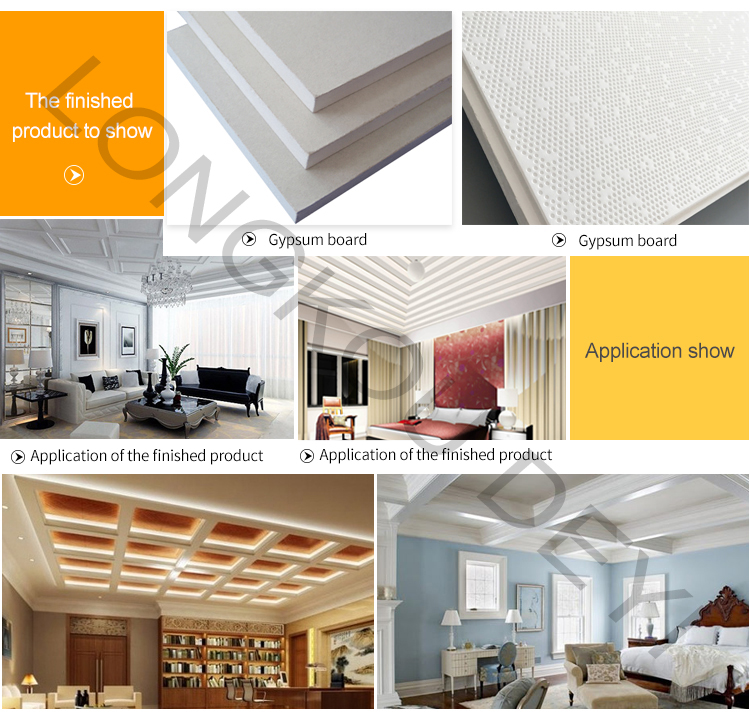
Production Process
1.Material Dosing section
In our gypsum board production line, the material dosing section is crucial. Our machinery for making gypsum board precisely measures raw materials like building gypsum, modified starch, and coagulant. After individual measurement, they’re mixed in a screw mixer. This well – blended mixture is then continuously fed into a vertical mixer. This step sets the quality base for the subsequent production, ensuring accurate ingredient proportions for high – quality gypsum boards.
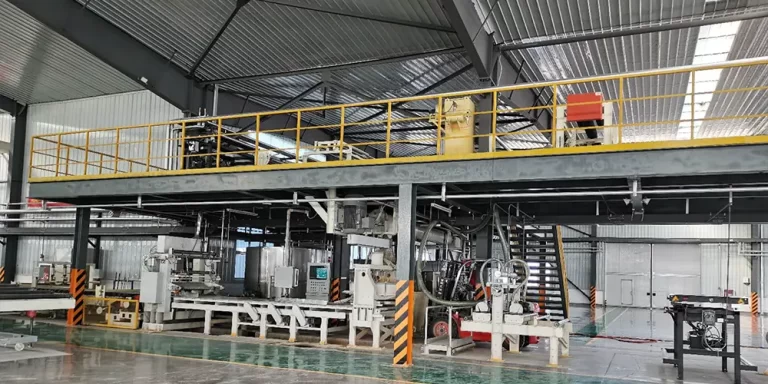
2.Forming section
The forming section of our gypsum board machine is where the board takes shape. Adhesive glue from a pot is fed to the sizing mouth of the forming station. It applies adhesive tape on both sides of the gypsum board top paper. The upper and under cover paper are transported to the paper rack by an electric hoist. This step creates the basic structure of the plasterboard, a key part of the overall production line.
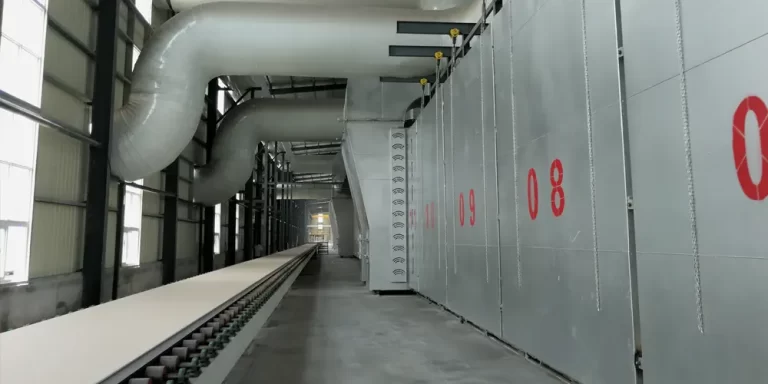
3.Drying section
Once formed, the boards enter the drying section. They’re sent to each layer of the 8 – layer dryer by a bridge distributor as per the program. The dryer uses natural gas – heated heat conduction oil as the heat source. With an air – duct system on top divided into two sections, it ensures efficient and uniform drying, enhancing the strength and durability of the gypsum boards.
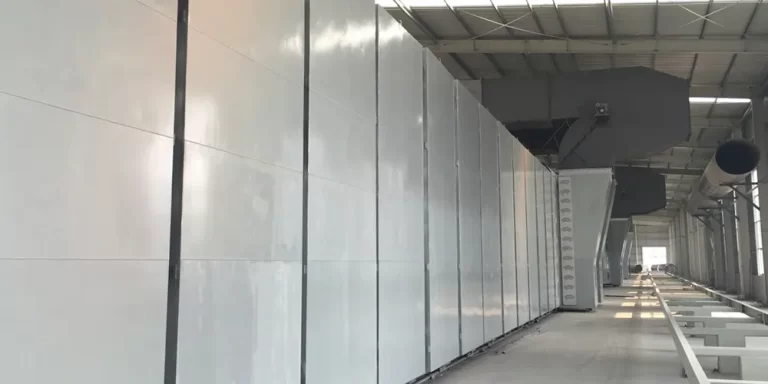
4.Edge cutting and stacking section
After drying, boards are sent to the edge – cutting machine via several conveyors. The machine cuts them to the required size. Then, a stacker piles the boards, and a forklift moves them to the finished – product warehouse for inspection and storage. This final step in our gypsum board production line prepares the products for market distribution.
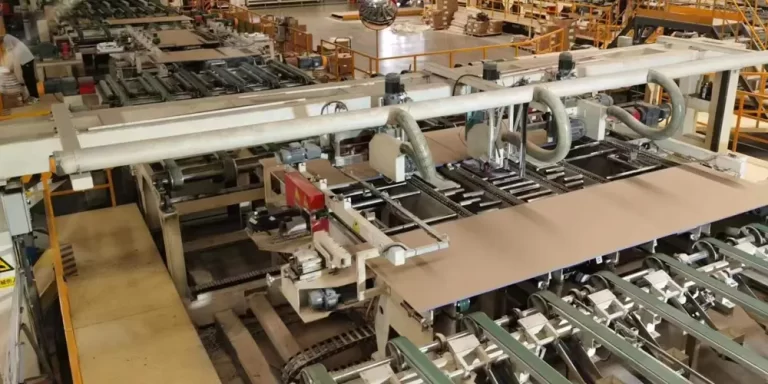
Lorem ipsum dolor sit amet, consectetur adipiscing elit. Ut elit tellus, luctus nec ullamcorper mattis, pulvinar dapibus leo.
Why Choose Our Production Line?
- Advanced Technology & Automation
Our gypsum board production line integrates cutting-edge automation for precise material dosing, forming, and drying. The machinery for making gypsum board uses screw and vertical mixers to ensure uniform slurry blending, while the 8-layer dryer with natural gas heat conduction oil guarantees efficient, energy-saving drying. - High-Quality Output
From plasterboard to fire-resistant and decorative variants, our line produces boards with consistent thickness (6mm–25mm) and strength. The adhesive application system ensures secure paper bonding, and edge-cutting machinery delivers exact dimensions for seamless installation. - Customization Flexibility
Adaptable to diverse raw materials (gypsum, additives) and market demands, our gypsum board machine supports custom board sizes and textures. Whether for residential partitions or commercial ceilings, the line meets global standards and design requirements. - Eco-Friendly & Cost-Effective
Energy-efficient components and optimized processes reduce operational costs and environmental impact. The construction material production line minimizes waste, while durable machinery ensures long-term reliability. - Turnkey Solutions
We provide comprehensive support: from installation and operator training to maintenance. Our team tailors configurations to your scale, ensuring a smooth transition to production.
Choose us for scalable, high-quality gypsum board manufacturing—backed by innovation and expertise
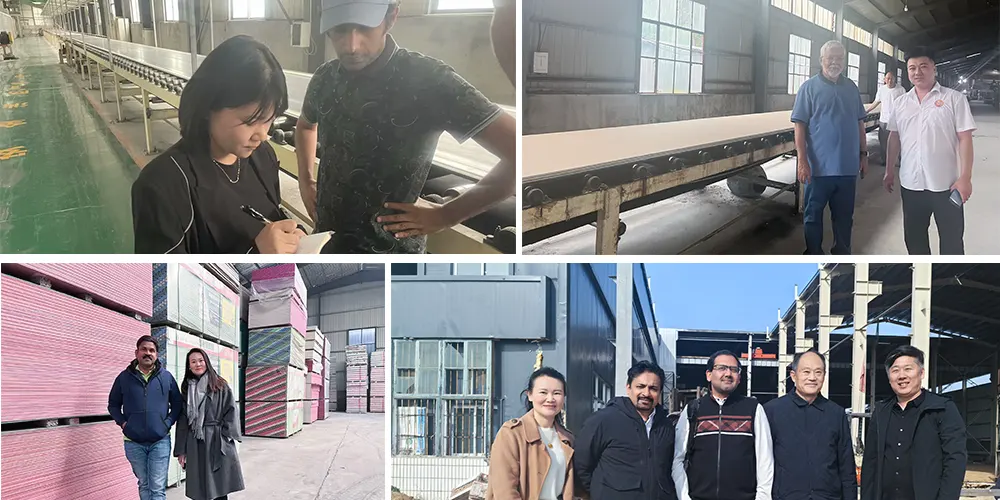